Everything about Alcast Company
Table of ContentsA Biased View of Alcast CompanyLittle Known Questions About Alcast Company.4 Simple Techniques For Alcast CompanyAlcast Company Fundamentals ExplainedGet This Report about Alcast CompanyAlcast Company Can Be Fun For Everyone
Chemical Contrast of Cast Aluminum Alloys Silicon promotes castability by lowering the alloy's melting temperature and enhancing fluidness throughout spreading. Additionally, silicon contributes to the alloy's toughness and use resistance, making it valuable in applications where resilience is critical, such as automobile components and engine elements.It also improves the machinability of the alloy, making it easier to process into completed items. In this means, iron adds to the general workability of light weight aluminum alloys.
Manganese adds to the toughness of light weight aluminum alloys and boosts workability (Aluminum Castings). It is generally made use of in functioned aluminum products like sheets, extrusions, and profiles. The presence of manganese aids in the alloy's formability and resistance to splitting during construction procedures. Magnesium is a lightweight element that provides stamina and influence resistance to aluminum alloys.
Rumored Buzz on Alcast Company
Zinc improves the castability of light weight aluminum alloys and helps regulate the solidification procedure during casting. It boosts the alloy's stamina and solidity.

The primary thermal conductivity, tensile stamina, return stamina, and prolongation differ. Amongst the above alloys, A356 has the highest possible thermal conductivity, and A380 and ADC12 have the lowest.
Indicators on Alcast Company You Should Know
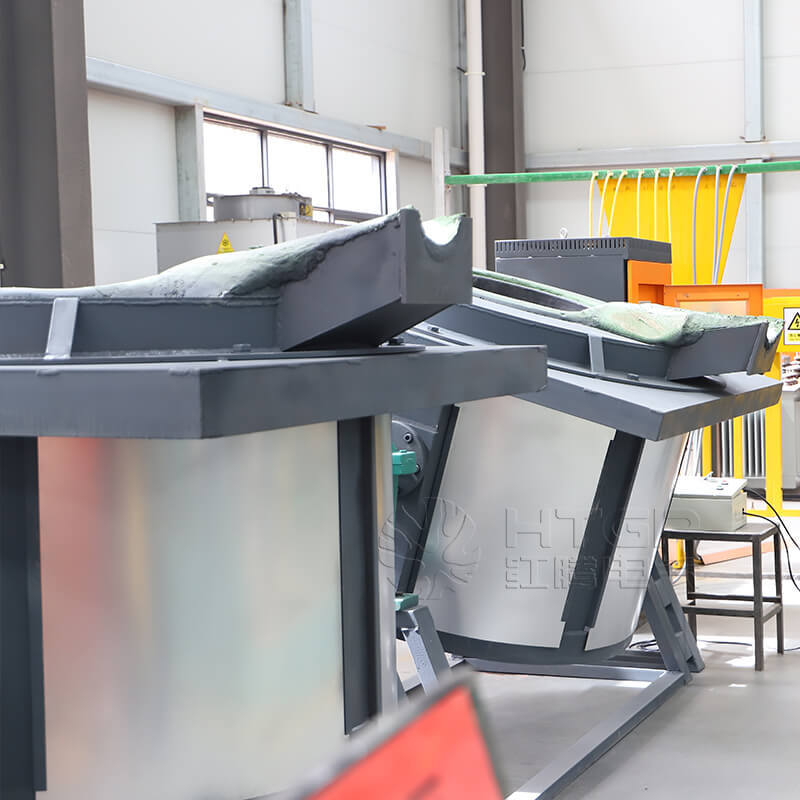
In precision casting, 6063 is well-suited for applications where intricate geometries and top notch surface my review here coatings are paramount. Instances include telecommunication enclosures, where the alloy's premium formability enables streamlined and cosmetically pleasing styles while maintaining architectural stability. Similarly, in the Illumination Solutions market, precision-cast 6063 elements develop elegant and efficient lights fixtures that need intricate shapes and great thermal performance.
The A360 shows exceptional prolongation, making it perfect for facility and thin-walled elements. In precision casting applications, A360 is fit for sectors such as Customer Electronic Devices, Telecommunication, and Power Devices.
Some Of Alcast Company
Its special residential properties make A360 a useful choice for precision spreading in these markets, enhancing product durability and quality. Light weight aluminum alloy 380, or A380, is an extensively used casting alloy with numerous unique qualities. It offers excellent castability, making it an optimal choice for precision casting. A380 shows excellent fluidness when molten, guaranteeing detailed and thorough mold and mildews are precisely reproduced.
In accuracy casting, light weight aluminum 413 shines in the Customer Electronic Devices and Power Devices sectors. This alloy's superior corrosion resistance makes it a superb choice for outdoor applications, guaranteeing long-lasting, sturdy items in the mentioned industries.
The 15-Second Trick For Alcast Company
The aluminum alloy you pick will considerably affect both the casting process and the properties of the final product. Due to the fact that of this, you must make your decision thoroughly and take an informed strategy.
Establishing the most appropriate light weight aluminum alloy for your application will mean considering a large range of characteristics. These relative alloy characteristics comply with the North American Pass Away Spreading Organization's guidelines, and we've separated them right into 2 classifications. The very first category addresses alloy qualities that influence the manufacturing process. The 2nd covers characteristics affecting the residential or commercial properties of the end product.
The Alcast Company Statements
The alloy you choose for die spreading straight affects a number of facets of the casting procedure, like exactly how easy the alloy is to collaborate with and if it is susceptible to casting problems. Warm cracking, also called solidification fracturing, is a typical die casting issue for aluminum alloys that can cause inner or surface-level tears or cracks.
Particular light weight aluminum alloys are more susceptible to hot fracturing than others, and your selection should consider this. Another usual problem found in the die casting of light weight aluminum is pass away soldering, which is when the cast sticks to the die wall surfaces and makes ejection tough. It can harm both the cast and the die, so you need to look for alloys with high anti-soldering properties.
Rust resistance, which is already a notable quality of aluminum, can differ substantially from alloy to alloy and is an essential particular to consider relying on the environmental conditions your item will be revealed to (aluminum metal casting). Put on resistance is one more home typically looked for in light weight aluminum products and can differentiate some alloys